บริการ ลดต้นทุนและเพิ่มประสิทธิภาพ โดยการนำ TPS มาประยุกต์ใช้ ระบบการผลิตแบบโตโยต้า คือระบบการผลิตที่มีชื่อเสียงและได้รับการยอมรับเป็นที่รู้จักในระดับสากลที่ทำให้ TOYOTA สามารถเป็นผู้นำในการผลิตรถยนต์ในระดับโลก เราให้บริการ เพิ่มประสิทธิภาพในการปฏิบัติงานโดยการนำระบบ Toyota Production System (TPS) มาประยุกต์ใช้ ยินดีให้คำปรึกษา
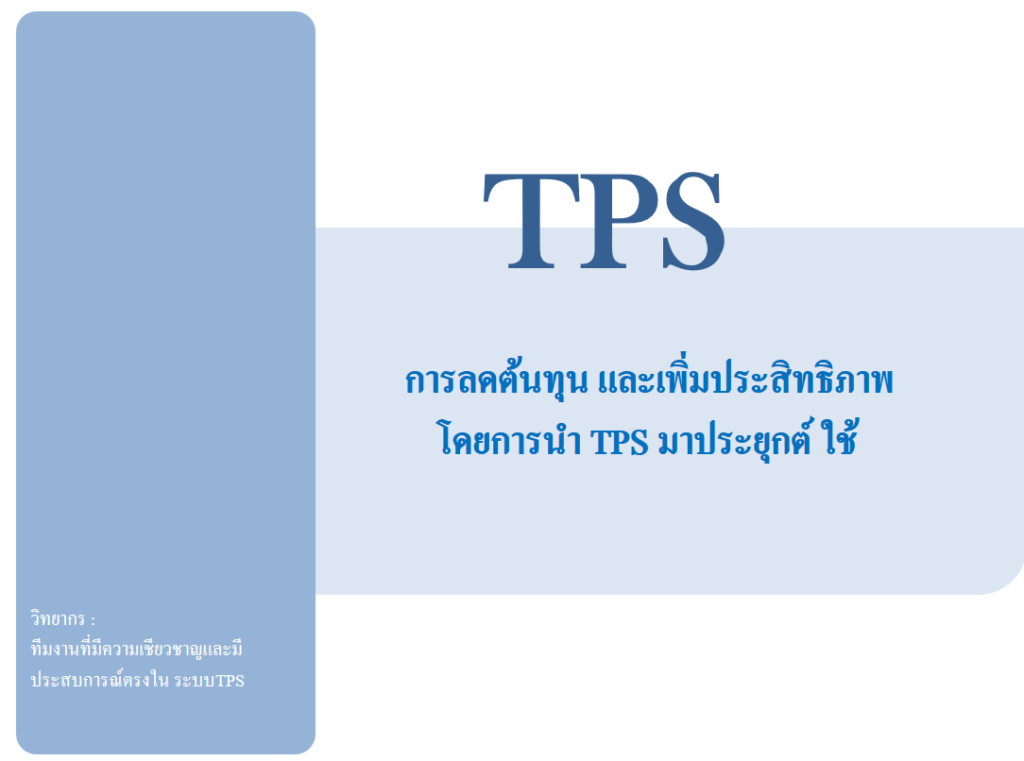
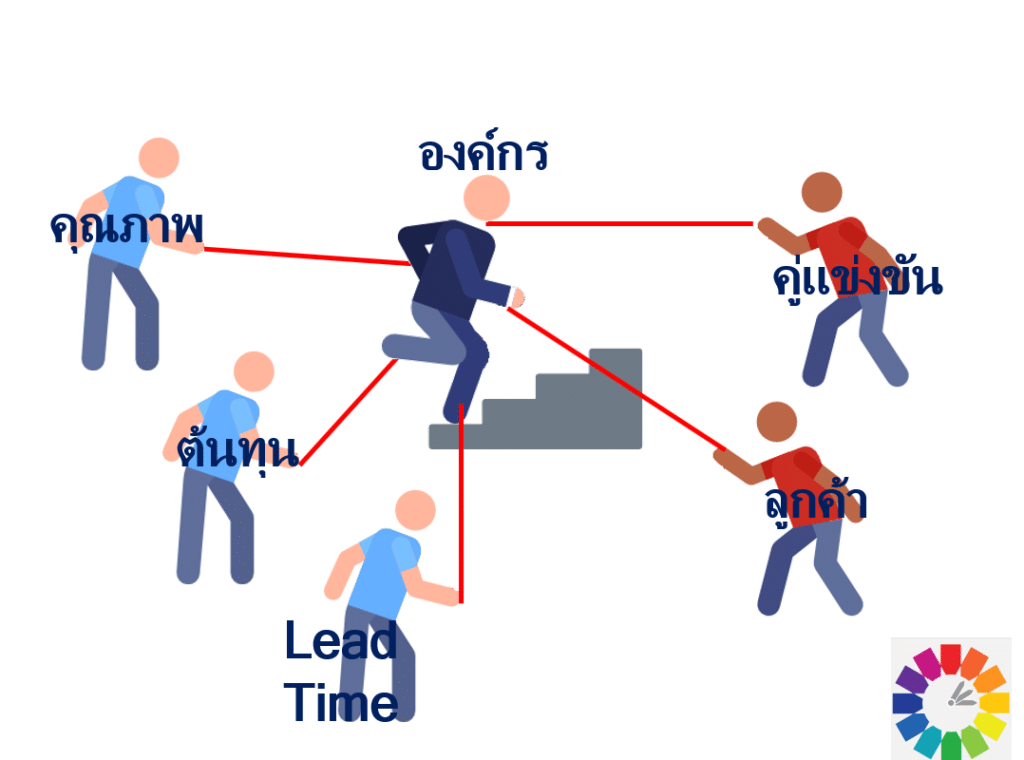

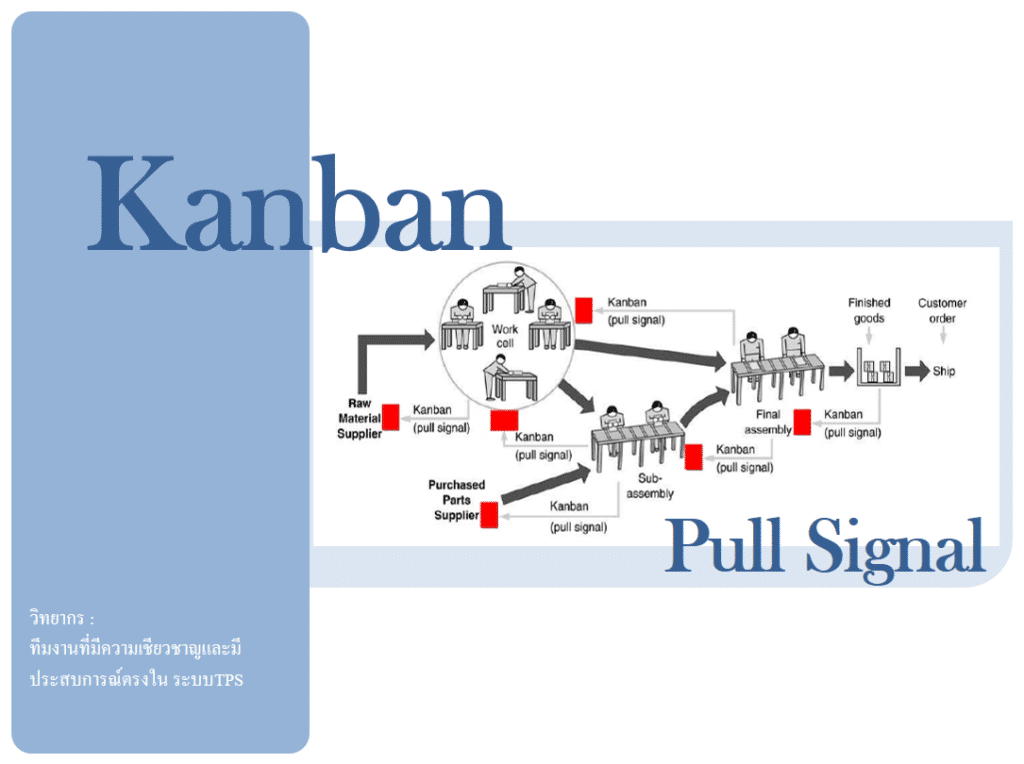
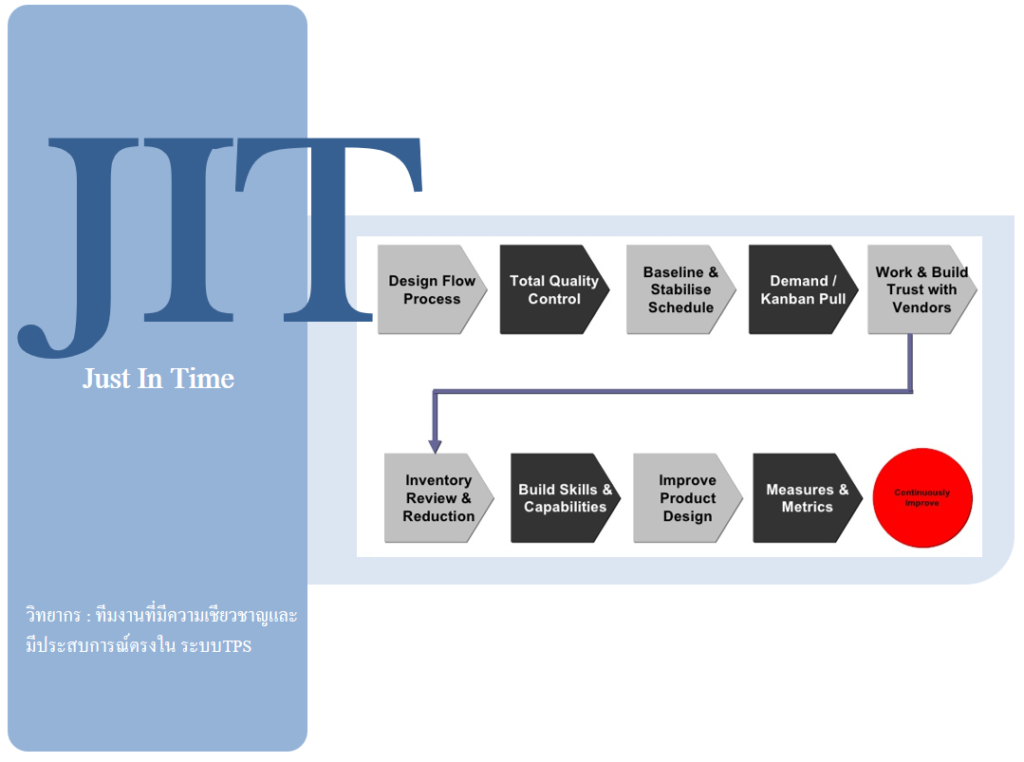
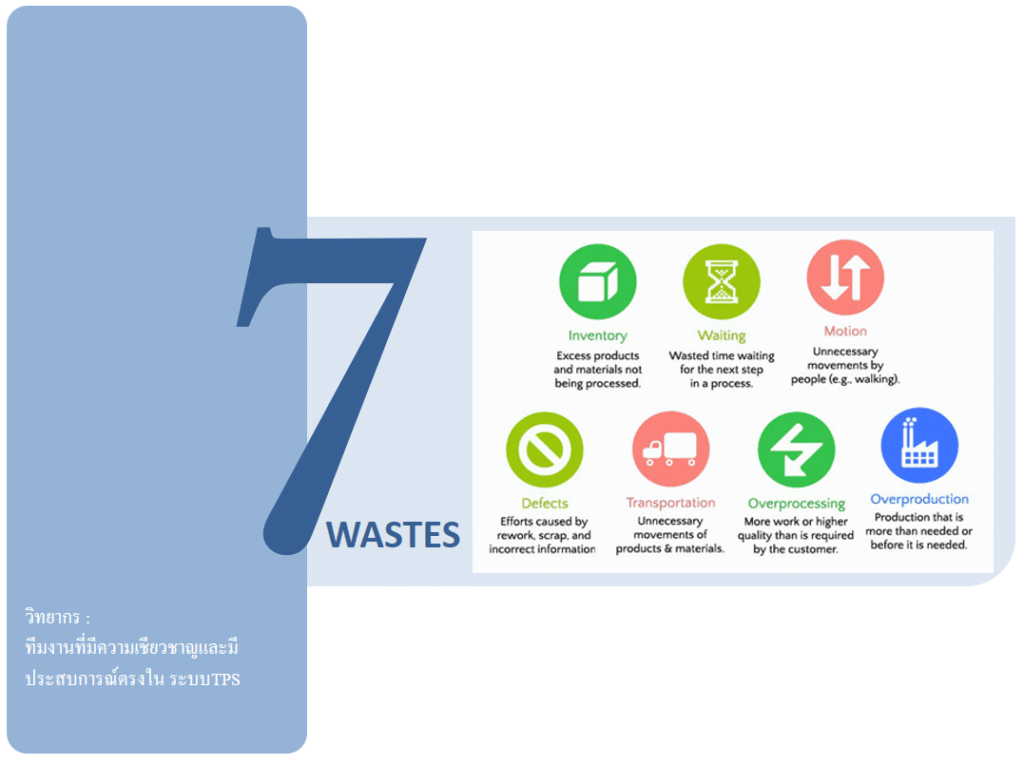
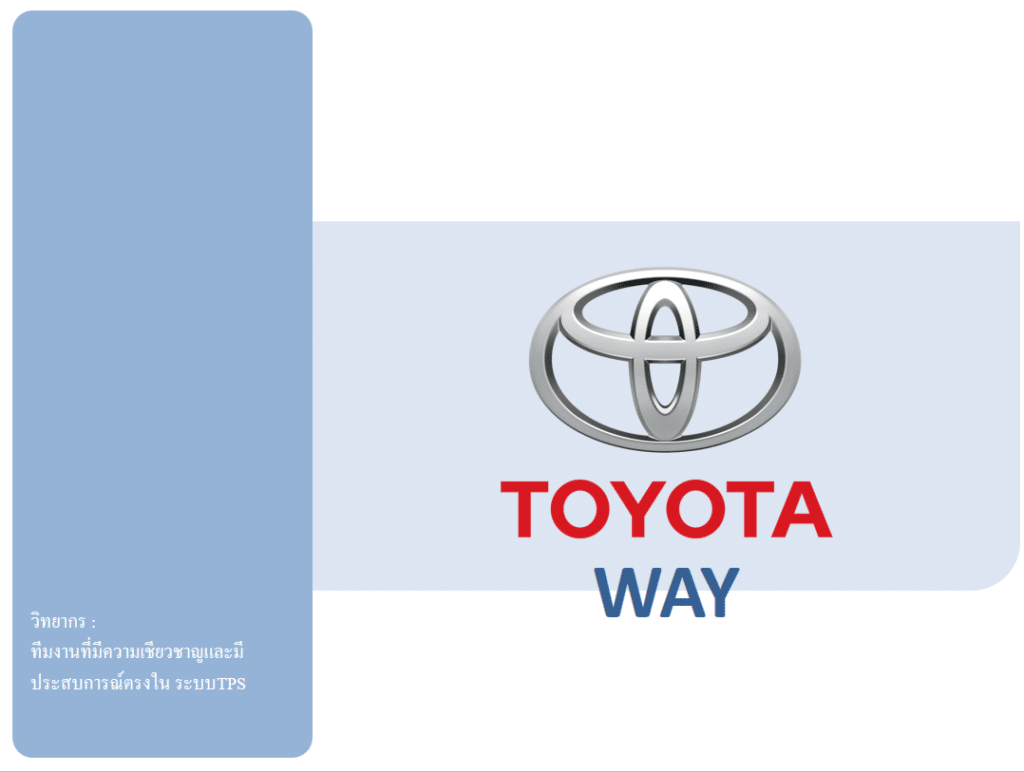
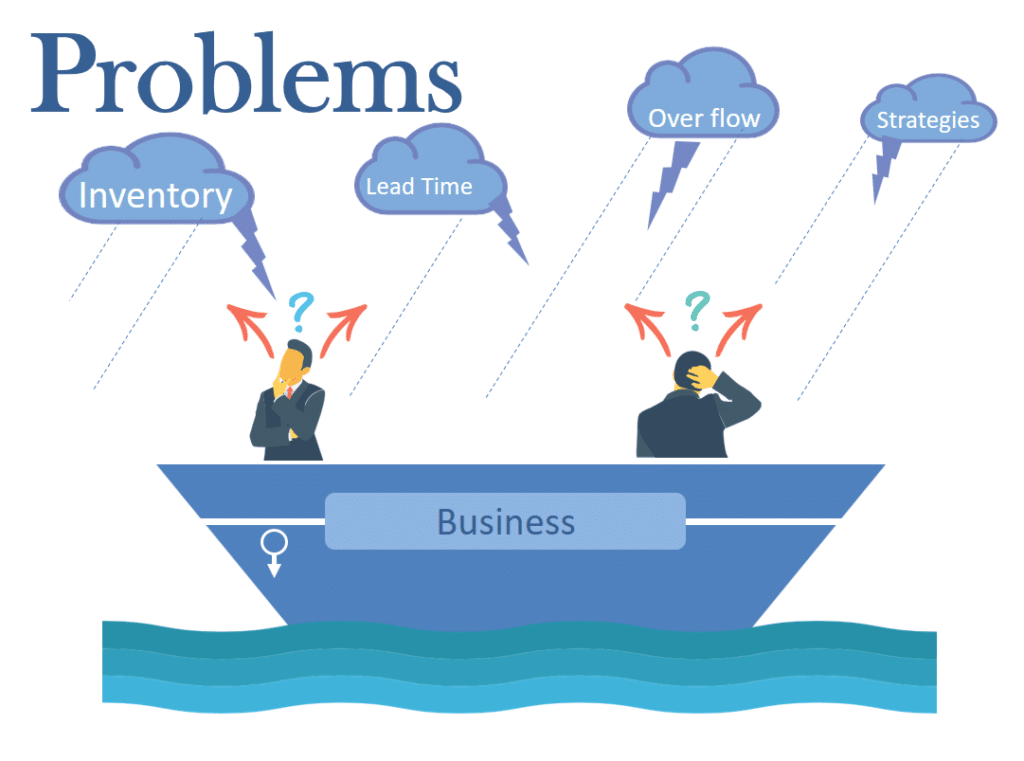
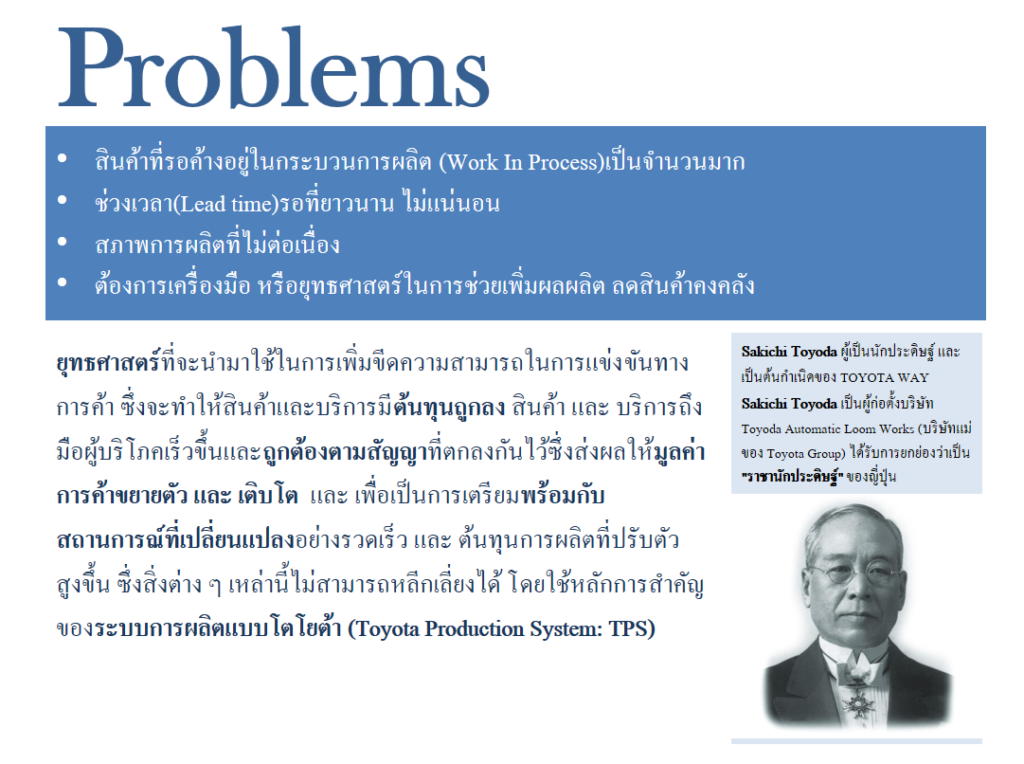
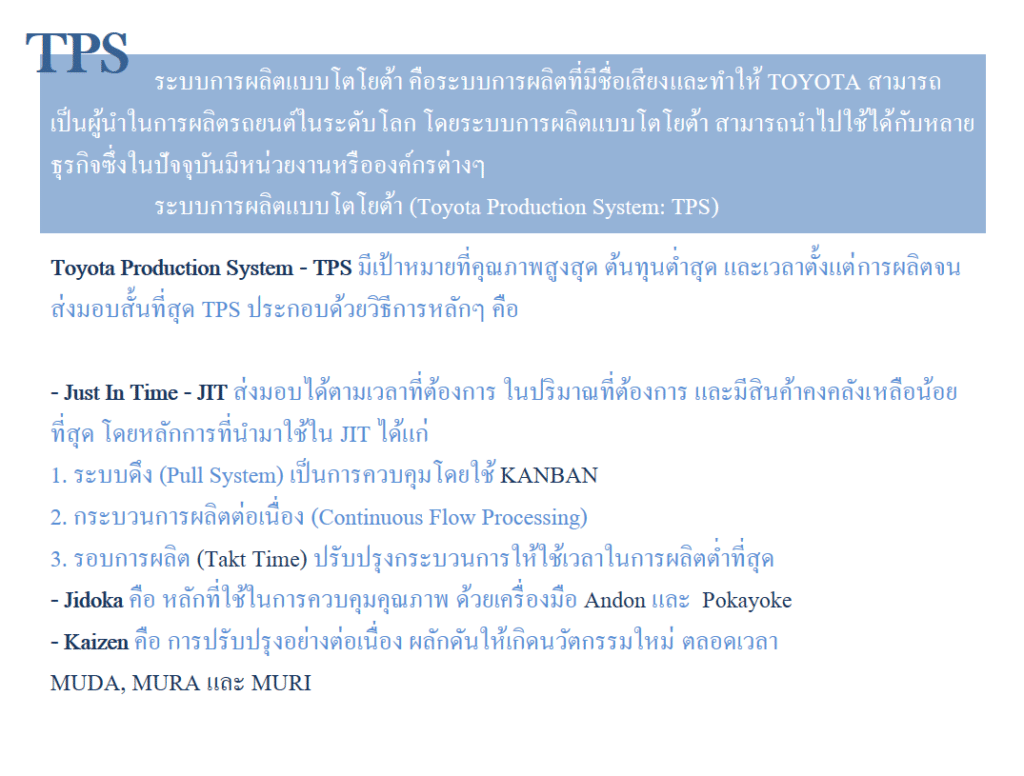
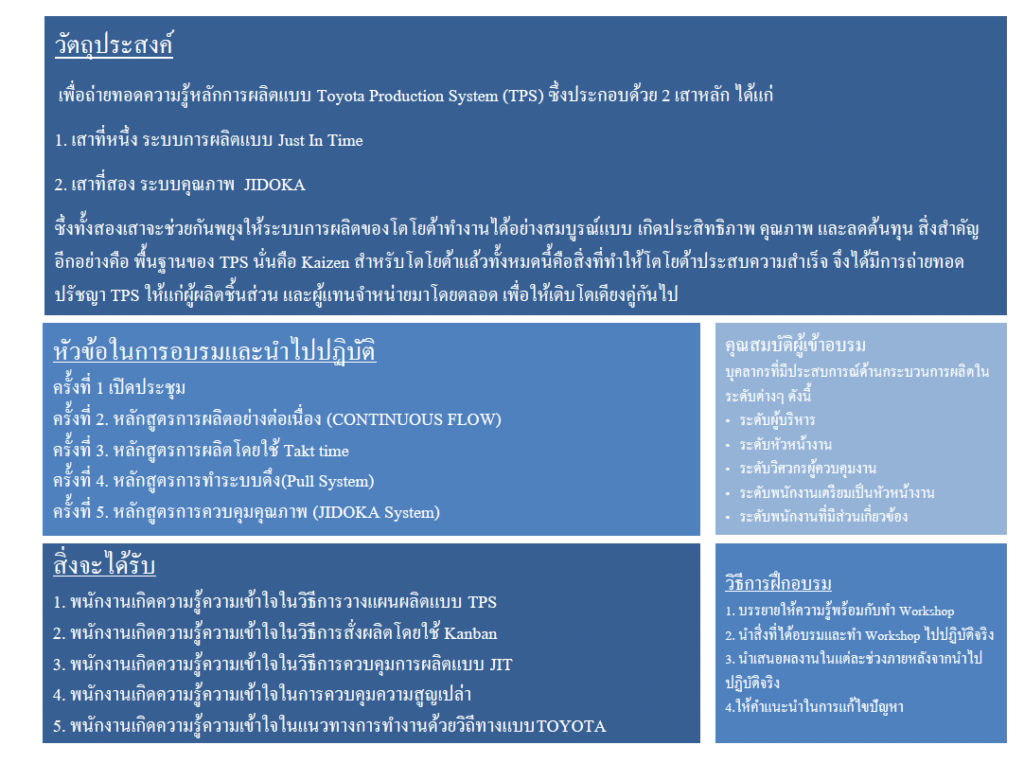
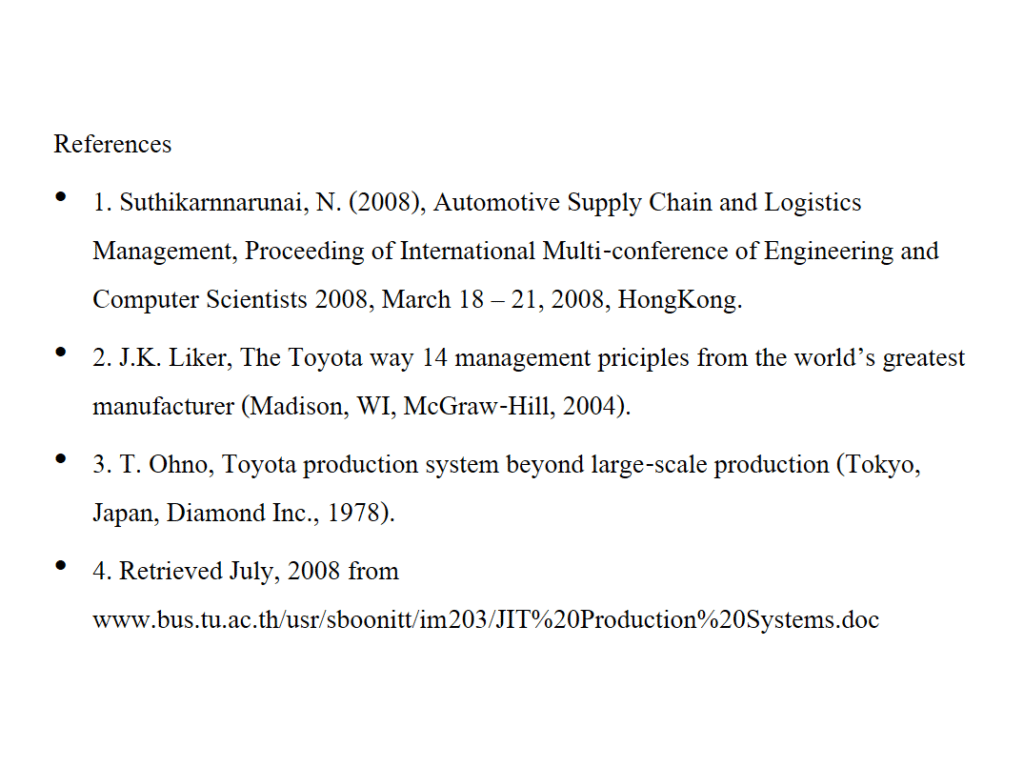
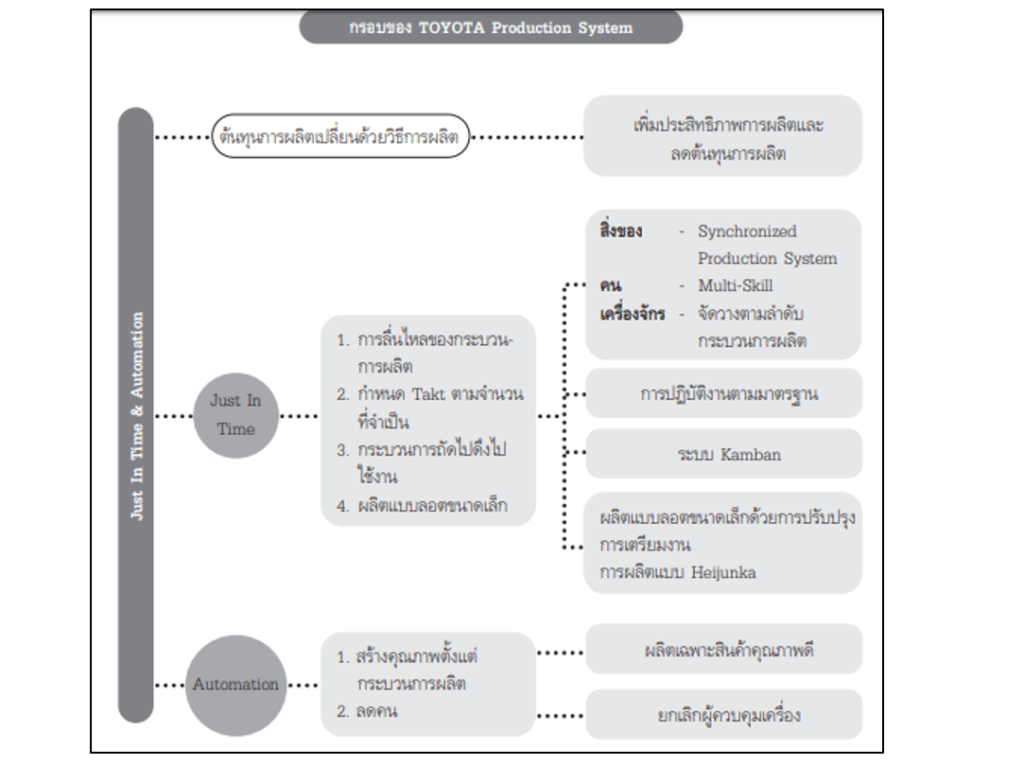
ระบบการผลิตแบบโตโยต้า คือระบบการผลิตที่มีชื่อเสียงและได้รับการยอมรับเป็นที่รู้จักในระดับสากลที่ทำให้ TOYOTA สามารถเป็นผู้นำในการผลิตรถยนต์ในระดับโลก โดยระบบการผลิตแบบโตโยต้า สามารถนำไปใช้ได้กับหลายธุรกิจซึ่งในปัจจุบันมีหน่วยงานหรือองค์กรต่างๆ ได้พยายามจะนำระบบการผลิตแบบโตโยต้าไปปฏิบัติ แต่อย่างไรก็ตามยังไม่มีหน่วยงานใดหรือองค์กรใดที่ประสบความสำเร็จเหมือนดังเช่นโตโยต้า
ระบบการผลิตแบบโตโยต้า (Toyota Production System: TPS) คือ ระบบการผลิตที่มุ่งเน้นในเรื่องการกำจัดความสูญเปล่าเพื่อลดต้นทุนการผลิตโดยยึดหลักการ ผลิตสินค้าที่ลูกค้าต้องการ ในเวลาที่ต้องการ และในจำนวนที่ต้องการเท่านั้น เพื่อควบคุมสินค้าคงคลังในจำนวนที่จำเป็นหรือของส่วนเกินต่างๆ จากกระบวนการผลิต
TOYOTA มองว่าสินค้าที่ผลิตแล้วขายไม่ได้ถือเป็นต้นทุนที่สูญเปล่าชนิดหนึ่ง ด้วยปรัชญาการผลิตเพื่อไม่ให้เกิดของเหลือหรือของส่วนเกินนี้เองทำให้ TOYOTA สามารถผลิตรถยนต์ได้โดยมีต้นทุนในการผลิตที่ต่ำและสามารถแข่งขันได้กับผู้ผลิตรถยนต์รายอื่นๆ
หลักการสำคัญในการลดต้นทุนการผลิตของ TOYOTA คือ Just In Time (JIT) และ JIDOKA แสดงดังรูปที่ 1
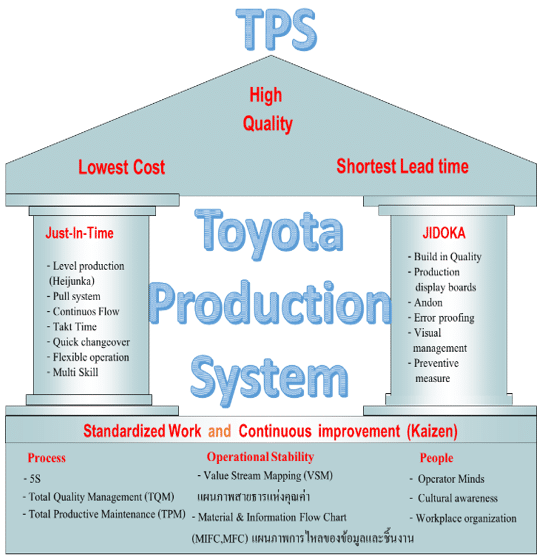
รูปที่ 1 ระบบการผลิตแบบ TOYOTA (Toyota Production System)
Just-In-Time
Just-In-Time ในความหมายที่ตรงตัว หมายถึง ทันเวลาพอดี ทำงานให้พอดีเวลา วางแผนให้ดี เตรียมการให้พอดี สำหรับระบบการผลิตแบบ Just In Time หรือระบบการผลิตแบบทันเวลาพอดีของ TOYOTA หมายถึง การผลิตหรือส่งมอบ สิ่งที่ต้องการ ในเวลาที่ต้องการ ด้วยจำนวนที่ต้องการ โดยใช้ความต้องการของลูกค้าเป็นเครื่องกำหนดปริมาณการผลิตและการใช้วัตถุดิบ และใช้ Pull System ในการควบคุมวัสดุคงคลัง และสินค้าคงคลัง และกระบวนการผลิต ทำให้ไม่เกิดของเหลือหรือของส่วนเกินทั้งในส่วนของวัตถุดิบ งานระหว่างทำ และสินค้าสำเร็จรูป
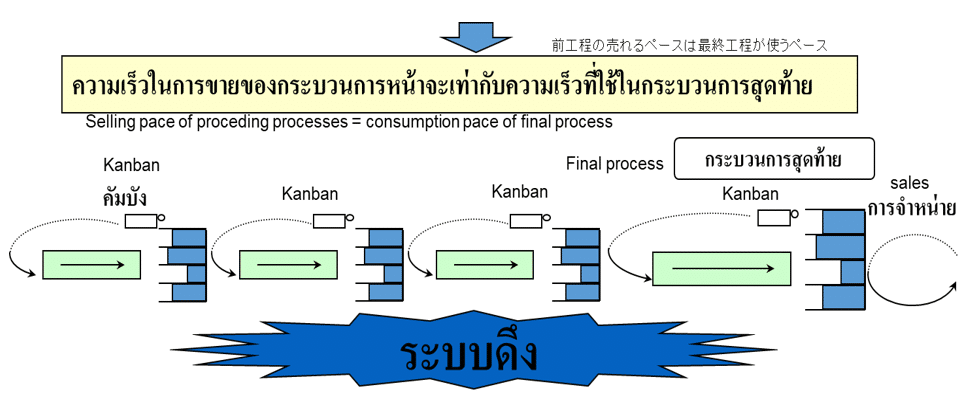
ระบบการผลิตแบบ Just In Time จะเริ่มต้นจากขั้นตอนของปรับให้สายการผลิตมีความราบเรียบสม่ำเสมอในทุกขั้นตอน หรือที่เรียกว่าการทำงานแบบ Heijunka หรือในภาษาอังกฤษเรียกว่า Leveled Production ในขั้นตอนนี้ระยะเวลาการผลิตในแต่ละกระบวนการจะถูกควบคุมด้วยระบบ Takt Time เพราะปัจจุบันนี้กระบวนการผลิตรถยนต์ในแต่ละสาย (Line) การผลิตได้เปลี่ยนแปลงจากเดิมมากโดยสายการผลิตแต่ละสายอาจประกอบด้วยการผลิตรถยนต์หลายๆ รุ่นในเวลาเดียวกัน ดังนั้นจะเห็นได้ว่าความต่อเนื่องของการผลิต (Continuous Flow Processing) ในแต่ละขั้นตอนมีส่วนสำคัญอย่างยิ่งที่จะทำให้ระบบ Just In Time ประสบความสำเร็จ
ระบบคัมบัง (Kanban System) เป็นอีกระบบหนึ่งที่ถือได้ว่าเป็นส่วนหนึ่งของระบบ JIT ที่ได้รับการพัฒนาขึ้นมาเพื่อช่วยให้การทำงานมีการประสานงานที่ดีและมีประสิทธิภาพ
ระบบคัมบังของโตโยต้า หรือ “Two-card System” จะใช้แผ่นกระดาษ เพื่อเป็นสัญญาณแสดงความต้องการให้มีการส่งชิ้นส่วนเพิ่มเติม (PW Kanban), (Conveyance Kanban : C – Card )
และใช้แผ่นกระดาษเดียวกันหรือที่มีลักษณะเหมือนกันเพื่อเป็นสัญญาณแสดงความต้องการให้ผลิต ชิ้นส่วนเพิ่มขึ้น (PI Kanban), (Production Kanban : P – Card ) ซึ่งบัตรนี้จะติดไปกับภาชนะ
( Packaging ) ที่ใส่วัตถุดิบซึ่งหลักการดำเนินงานของระบบ Kanban นั้นจะต้องประกอบด้วยหลักการต่างๆ ที่สำคัญดังต่อไปนี้
- ในแต่ละภาชนะจะต้องมี Kanban อยู่ด้วยเสมอ
- หน่วยงานประกอบจะเป็นผู้เบิกจ่ายชิ้นส่วนจากหน่วยผลิตโดยระบบดึง
- ถ้าไม่มีใบเบิกที่มีคำสั่งอนุมัติจะไม่มีการเคลื่อนภาชนะออกจากที่เก็บ
- ภาชนะจะต้องบรรจุชิ้นส่วนในปริมาณที่ถูกต้องและมีคุณภาพที่ดีเท่านั้น
- ชิ้นส่วนที่ดีเท่านั้นที่จะถูกจัดส่งและใช้งานในสายการผลิต
- ผลผลิตรวมจะไม่มากเกินไปกว่าคำสั่งผลิตที่ได้บันทึกลงใน P-Card และวัตถุดิบที่เบิกใช้จะต้องไม่มากกว่าจำนวนชิ้นส่วนที่บันทึกใน C-Card
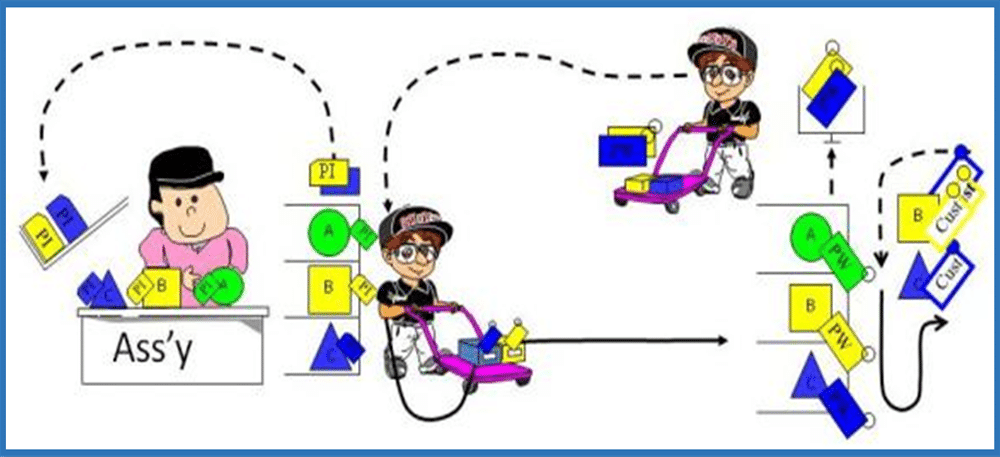
รูปที่ 2 ตัวอย่างของการปฏิบัติงานด้วยระบบ Kanban
รูปที่ 2 แสดงถึงตัวอย่างของการปฏิบัติงานด้วยระบบ Kanban ที่แสดงถึงสายการประกอบหนึ่ง มีชิ้นส่วน A และ B เป็นชิ้นส่วนหลักสำหรับการผลิต ชิ้นส่วน A และชิ้นส่วน B เมื่อถูกผลิตขึ้นแล้วจะเก็บไว้ที่คลังข้างหน่วยผลิต และคัมบังสั่งผลิตจะถูกติดไว้กับชิ้นส่วนที่ผลิตขึ้นนี้พนักงานจะขนของจากสายประกอบซึ่งกำลังประกอบผลิตภัณฑ์ A จะไปยังคลังของหน่วยผลิตเพื่อเบิกถอนชิ้นส่วน A เท่าที่จำเป็นโดยนำคัมบังเบิกถอนไปด้วย และที่คลังของชิ้นส่วน A จะหยิบกล่องบรรจุชิ้นส่วน A ตามจำนวนของคัมบังเบิกถอน และจะปลดคัมบังสั่งผลิตที่ติดอยู่กับชิ้นส่วน A ออกจากกล่องเหล่านี้ไว้ที่คลัง จากนั้นเขาก็จะนำกล่องชิ้นส่วน A ไปยังสายประกอบพร้อมกับคัมบังเบิกถอน ในเวลาเดียวกันคัมบังสั่งผลิตที่โดนปลดไว้ที่คลังชิ้นส่วน A ของหน่วยผลิตจะแสดงถึงจำนวนหน่วยของชิ้นส่วนที่โดนเบิกถอนไป บัตรคัมบังเหล่านี้จะเป็นเสมือนคำสั่งผลิตให้แก่หน่วยผลิตในกระบวนการต่อไป ซึ่งชิ้นส่วน A ก็จะถูกผลิตขึ้นตามจำนวนบัตรคัมบังสั่งผลิตตามปกติในหน่วยผลิตดังกล่าว ชิ้นส่วน A และชิ้นส่วน B จะถูกเบิกถอนไปทั้งคู่แต่ชิ้นส่วนเหล่านี้จะถูกผลิตขึ้นตามลำดับการปลดออกของคัมบังสั่งผลิต หรืออีกนัยหนึ่งคือตามลำดับการเบิกถอนของชิ้นส่วนโดยสายประกอบนั่นเอง
วัตถุประสงค์หลักของระบบการผลิตแบบ Just In Time นั้นมีดังต่อไปนี้
- ให้มีวัสดุคงคลัง (stock) ประเภทต่างๆ อยู่ในระดับที่น้อยที่สุดหรือไม่มีอยู่เลย เพื่อให้ไม่เกิด
- ต้นทุนการจัดเก็บ ต้นทุนค่าเสียโอกาส
- ลดเวลารอคอยในกระบวนการต่างๆ ให้เหลือน้อยที่สุดหรือไม่ต้องรอคอยเลยเพื่อไม่ให้เกิด
- เวลาว่างเปล่าของพนักงานและอุปกรณ์ และให้เกิดประสิทธิภาพเต็มที่
- ขจัดของเสียที่เกิดขึ้นจากกระบวนการผลิตที่ไม่จำเป็น
- ขจัดความสูญเปล่า 7 ประการในกระบวนการผลิต ได้แก่
ไม่ผลิตมากเกินไป ไม่เกิดการรอคอยระหว่างการผลิต ไม่เกิดการเคลื่อนย้ายวัสดุในระยะทางที่มากเกินไป ไม่เกิดการปฏิบัติงานที่ไม่จาเป็น ไม่มีวัตถุดิบหรือผลิตภัณฑ์สำเร็จรูปมากเกินไป ไม่มีการเคลื่อนไหวที่ไม่จำเป็นของผู้ปฏิบัติงาน และไม่มีการผลิตผลิตภัณฑ์ที่ไม่มีคุณภาพ
ซึ่งประโยชน์ของการใช้ระบบการผลิตแบบทันเวลาพอดีหรือ Just In Time นั้นมีมากมายหลายประการด้วยกัน นอกเหนือจากจะสามารถลดต้นทุนการจัดเก็บ และต้นทุนค่าเสียโอกาสแล้ว ยังเป็นการยกระดับคุณภาพสินค้าให้สูงขึ้น ลดของเสียจากการผลิตให้ลดน้อยลง ระบบการผลิตมีความคล่องตัวมากขึ้น ระยะเวลาในการผลิตรวมน้อยลง ระบบการพยากรณ์ในการผลิตแม่นยำมากขึ้น สามารถตอบสนองความต้องการของลูกค้าได้เร็วขึ้น คนงานมีส่วนร่วมในการทำงานและมีความรับผิดชอบในงานมากขึ้น และคนงานทำงานอย่างมีประสิทธิภาพมากขึ้น
JIDOKA
JIDOKA หรือในความหมายของคำภาษาอังกฤษว่า “Autonomation” หมายความว่า การควบคุมตัวเองโดยอัตโนมัติ ในความหมายของ TOYOTA คือ การใช้เครื่องมือหรือเครื่องจักรในการป้องกันความผิดพลาดในการทำงานที่อาจจะทำให้สินค้าเสียเกิดขึ้น หรือในทุกๆกระบวนการหากเกิดการผิดพลาดขึ้นจะมีระบบอัตโนมัติเพื่อหยุดยั้งการส่งสินค้าที่มีความเสียหายหรือคุณภาพไม่ได้มาตรฐานไปยังกระบวนการต่อไปซึ่งอาจจะส่งผลให้เกิดการผลิตสินค้าสำเร็จรูปที่ไม่ได้คุณภาพหรือไม่ได้มาตรฐานส่งไปถึงมือลูกค้าได้ หรืออาจกล่าวอย่างสั้นๆ ได้ว่าระบบ JIDOKA คือกระบวนการควบคุมตัวเองโดยอัตโนมัติเพื่อป้องกันข้อผิดพลาดที่อาจเกิดขึ้นในสายการผลิตหรือในเครื่องจักร ในทางปฏิบัติของ TOYOTA ระบบ JIDOKA จะเริ่มจากการติดตั้งสัญญาณไฟฟ้า (Andon) ที่จะบอกชื่อรถ รุ่น และข้อมูลต่างๆ ที่จะทำให้พนักงานทราบว่าจะต้องประกอบชิ้นส่วนใดบ้าง อะไหล่ใดบ้าง หากพบข้อผิดพลาดที่ไม่จำเป็นต้องมีการหยุดสายการผลิต เช่น พนักงานใส่หรือประกอบชิ้นส่วนผิดพลาดจากที่กำหนดไว้ สัญญาณเตือนจะดังขึ้นทันที แต่หากว่ามีเหตุการณ์ฉุกเฉินเกิดขึ้นบริษัทได้มีระบบที่เรียกว่า การกำหนดจุดหยุด (Fixed Position Stop System) ไว้ โดยพนักงานสามารถดึงสัญญาณนี้เพื่อเป็นการเรียกให้หัวหน้างานได้สามารถเข้ามาตรวจสอบและแก้ไขได้ทันท่วงที นอกจากนั้น ณ ขั้นตอนสุดท้ายของระบบนั้นยังมีระบบที่เรียกว่า POKAYOKE หรือเครื่องมือที่ป้องกันสถานการณ์อันผิดปกติอันอาจเป็นเหตุให้เกิดปัญหาได้ก่อนที่จะส่งต่อไปยังระบบอื่นๆ
ข้อดีของระบบ Jidoka นั้น ไม่เพียงแต่จะช่วยให้ไม่มีสินค้าเสียหายหรือไม่ได้มาตรฐานเกิดขึ้นเท่านั้น แต่จะช่วยให้การไหลของวัสดุในระบบ JIT ทำได้อย่างมีประสิทธิภาพด้วยซึ่งจะช่วยลดเวลาการทำงาน และป้องกันการเกิดของเสีย (Waste) ในระบบ เช่น การเสียเวลาตรวจสอบสินค้า การรอคอย การขนส่ง และสินค้าเสียหายหรือคุณภาพไม่ได้มาตรฐาน
ซึ่งหลักการ 3 ประการที่สำคัญของ Jidoka
คือ การแยกการทำงานของพนักงานกับการทำงานของเครื่องจักรออกจากกัน การพัฒนาอุปกรณ์หรือเครื่องมือเพื่อป้องกันการทำให้สินค้าเสียหายหรือไม่ได้คุณภาพ และการประยุกต์ใช้ Jidoka กับกระบวนการประกอบชิ้นส่วนต่าง ๆ
นอกจากนี้ TOYOTA ยังได้ระบุด้วยว่าสาเหตุสำคัญที่ทำให้คุณภาพในการผลิตลดลงนั้น มี 3 สาเหตุหลักด้วยกัน คือ
- MUDA คือ ความสูญเปล่าที่ไม่เกิดคุณค่า
- MURI คือ การรับภาระเกินความสามารถของบุคคลและอุปกรณ์
- MURA คือ การผลิตที่ไม่สม่ำเสมอ
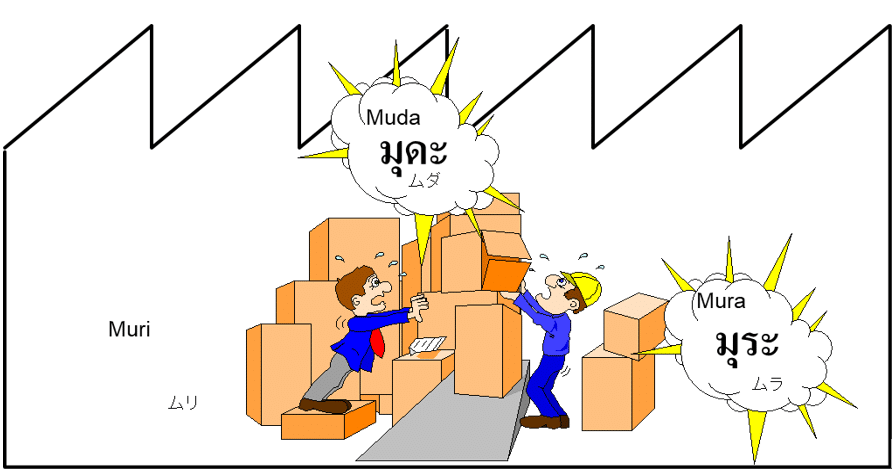
นอกเหนือจากระบบการผลิตแบบ Just In Time และ Jidoka อันโด่งดังแล้ว TOYOTA ยังมีชื่อเสียงในเรื่องของระบบการประกันคุณภาพ (Quality Assurance : QA) ในระดับโลกซึ่งในระบบ QA ของ TOYOTA นี้จะเริ่มตั้งแต่เริ่มผลิตสินค้าจนถึงส่งมอบลูกค้า และยังรวมถึงกระบวนการแก้ปัญหาให้แก่ลูกค้าเมื่อลูกค้าพบปัญหาจากตัวสินค้าของ TOYOTA
โดยนโยบายด้านคุณภาพของ TOYOTA คือ การสร้างความพึงพอใจสูงสุดให้แก่ลูกค้าโดยการสร้างระบบการประกันคุณภาพในกระบวนการผลิต (Built in Quality) ซึ่ง TOYOTA ได้กำหนดให้พนักงานทุกคนได้รับการฝึกอบรมให้เป็นทั้งผู้ปฏิบัติงานและผู้ตรวจสอบงานเพื่อสร้างและปลูกฝังให้ทุกคนได้มีส่วนร่วมในการควบคุมกระบวนการผลิตทุกกระบวนการ
นอกเหนือจากระบบการผลิตที่เป็นเลิศของ TOYOTA แล้วหัวใจสำคัญของ TOYOTA ที่ทำให้ TOYOTA ประสบความสำเร็จอย่างยิ่งใหญ่ในระดับโลกและไม่มีคู่แข่งรายได้สามารถแข่งขันได้ในปัจจุบันนั้น คือ วัฒนธรรมองค์กรที่ถูกหล่อหลอมให้เป็นปรัชญาในการทำงานร่วมกัน และเป็นพฤติกรรมการปฏิบัติร่วมกันขององค์กร หรือที่เรียกกันว่าหลักการ TOYOTA WAY ที่ประกอบด้วยหลักสำคัญ 5 ประการ ได้แก่ ความท้าทาย (Challenge) ไคเซ็น (Kaizen) เก็นจิ เก็นบุตซึ (Genchi Genbutsu) การยอมรับนับถือ (Respect) และการทำงานเป็นทีม (Teamwork) สิ่งจะได้รับ
- เกิดความรู้ความเข้าใจในวิธีการวางแผนผลิตแบบ TPS
- เกิดความรู้ความเข้าใจในวิธีการสั่งผลิตโดยใช้ Kanban
- เกิดความรู้ความเข้าใจในวิธีการควบคุมการผลิตแบบ JIT
- เกิดความรู้ความเข้าใจในการควบคุมความสูญเปล่า และการลดต้นทุนอย่างเป็นระบบ
- เกิดความรู้ความเข้าใจในแนวทางการทำงานด้วยวิถีทางแบบTOYOTA
ติดต่อบริการ ลดต้นทุนและเพิ่มประสิทธิภาพ โดยการนำ TPS มาประยุกต์ใช้ บริษัท กรีนโปร เคเอสพี แอคเคาท์ติ้ง จำกัด
32/8-9 หมู่ที่ 1 ถนนสุขาภิบาล 5 ซอย 73 แขวง ออเงิน เขต สายไหม กรุงเทพฯ 10220
โทร : 02-563-6187-8 แฟกซ์ : 02-563-6089
มือถือ : 081-648-7459
LINE ID : @greenprokspacc
E-mail : surapa@greenproksp.com